Material Sourcing
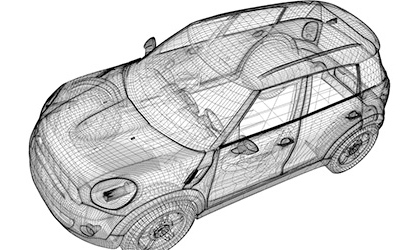
We provide a wide range of automotive materials and parts with solutions tailored to our customers' challenges, including the interior and exterior parts of automobiles, resin material of engine room, hoses/antivibration material/rubber material for window seals, as well as highly functional materials supporting electrification.
For more details, see Automobile Raw MaterialsMade-in-China Raw Materials
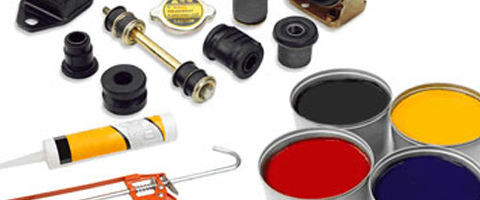
Our raw materials made in China have been been used in Japanese automobile parts, paints and adhesive markets mainly in China, but also shipped to Japan and ASEAN countries.
Unlike typical made-in-China materials, we offer materials that do not have foreign matter mixed or lot-to-lot difference.
Metal Sulfides
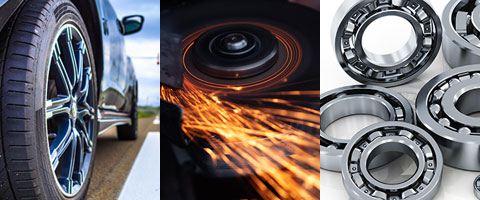
Our solid lubricants (metal sulfides) offer an extensive product line, which have been used in automobile parts and resin compounds. We provide materials that meet detailed requirements including particle size, appearance, and sliding properties.